Tomato paste is a staple ingredient in kitchens worldwide, finding its way into sauces, soups, and a myriad of other dishes. Given its high demand and versatile usage, establishing a tomato paste processing plant can be a lucrative venture. However, like any business endeavor, it requires careful consideration of costs and planning. Here, we break down the various cost involved in setting up tomato paste processing plant.
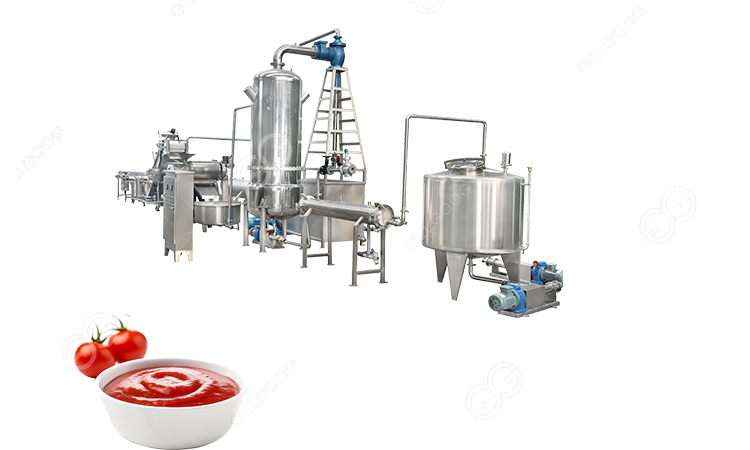
Initial investment
Land and building: Acquiring land and constructing or retrofitting a building suitable for processing operations is one of the significant upfront costs. Factors like location, size, and infrastructure can influence this expense.
Tomato paste making equipment: The heart of any processing plant lies in its machinery. Equipment such as pulpers, peelers, blanchers, evaporators, and packaging machines are essential for turning fresh tomatoes into paste efficiently. The cost of this machinery can vary depending on the capacity and technological sophistication.
Utilities and infrastructure: Installing utilities like water, electricity, and gas, as well as establishing proper drainage and waste disposal systems, are crucial aspects of plant infrastructure. These costs can vary based on local regulations and the scale of operations.
Operational costs
Raw materials: The primary input for tomato paste production is, of course, tomatoes. The cost of acquiring tomatoes can fluctuate based on factors like seasonal availability, local production, and quality.
Labor: Skilled and unskilled labor is required for various stages of processing, including sorting, washing, cooking, and packaging. Labor costs can significantly impact the overall operational expenses.
Utilities: Continuous operation of machinery requires significant amounts of water, electricity, and sometimes steam or gas. Monitoring and optimizing utility usage can help control operational costs.
Maintenance and repairs: Regular maintenance of machinery and infrastructure is necessary to ensure smooth operations and prevent breakdowns. Budgeting for ongoing maintenance and occasional repairs is crucial.
Regulatory and quality assurance costs
Regulatory compliance: Meeting regulatory standards for food safety and quality is non-negotiable in the food processing industry. Costs associated with obtaining permits, inspections, and ensuring compliance with health and safety regulations should be factored in.
Quality assurance: Implementing quality control measures throughout the production process is essential to maintain product consistency and meet consumer expectations. This includes costs for laboratory testing, quality inspections, and personnel training.
Marketing and distribution
Packaging: Packaging materials play a crucial role in preserving the quality of the product and attracting consumers. Costs for jars, cans, pouches, labels, and other packaging materials should be considered.
Marketing: Promoting the product through advertising, branding, and distribution channels is essential for market penetration and brand recognition. Marketing costs can vary depending on the chosen strategies and target markets.
Establishing a tomato paste processing plant requires a significant initial investment and ongoing operational expenses. However, with careful planning, efficient operations, and a focus on quality, it can be a profitable venture in the long run. Conducting a detailed cost analysis, considering factors like equipment, labor, utilities, regulatory compliance, and marketing, is essential for setting realistic expectations and ensuring the success of the business.