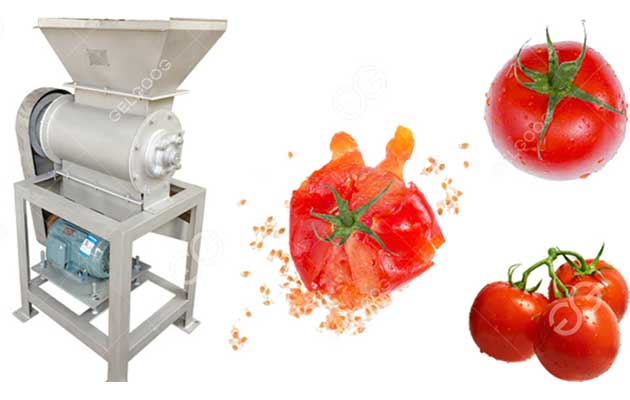
Tomato paste processing technology is usually divided into cold crushing process and hot crushing process. In recent years, some people have developed the thermal crushing process, so there are also super-high viscosity thermal crushing, “super hot crushing” and other process names. Only take a brief introduction of the difference between the two processes of tomato paste “cold break” and “hot break”
In the tomato sauce processing line, there is an indispensable part of “breaking”. Tomatoes are crushed after washing and sorting, and then sent to beating.
Strictly speaking, the terms “cold breaking” and “hot crushing” are not precise, because tomatoes are not heated when they are crushed by the tomato crusher, but are breaked at natural temperature.
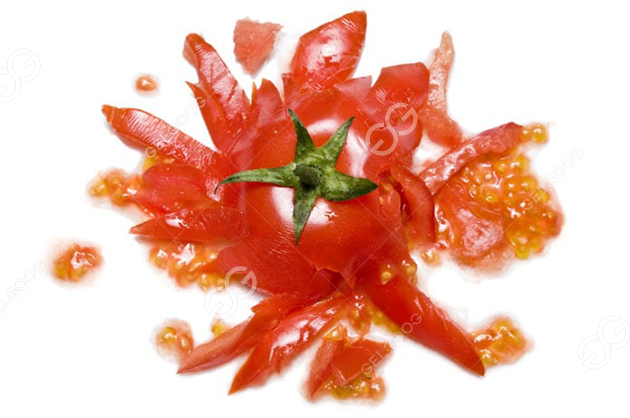
The commonly called cold breaking process is that the tomatoes are preheated immediately after crushing by tomato pre-heater, and then sent to be beaten immediately. The preheating temperature is below 60°C.
The commonly called thermal breaking process is to heat the tomatoes to B0~B5*C immediately after breaking, and then circulate heating in the thermal breaking system, and stay in the breaked material tank for a period of time, and then send to the beating treatment. The length of stay in tank is determined by the effective volume of the tank and the setting of the material liquid level, which can be adjusted as needed. Later, the heating temperature was increased to above 85°C and above 95°C. Recently, some manufacturers simply canned materials or sealed equipment that can withstand internal pressure. In this way, the heating temperature can theoretically be increased to more than 100 °C.
The main difference between the tomato paste “cold break” and “hot break” processes is the degree of heating of the material before the pulping treatment after the tomato is crushed and the elapsed time at that temperature.